Ok, so I decided to build my own 3d printer. But needs to be very cost effective, otherwise I can buy a new and pre-build one. But there is no fun in that.
I have an old Velleman K8400, it is build around/in a plexiglass case. And the case has started to weaken, but stepper motors, mainboard etc… are still working fine. So an idea was born.
I want to build a 3D printer, based on the K8400 parts, with modern firmware and a sturdy aluminium frame.
I am going to use 5 stages:
- Electronics/firmware PT1 on my Youtubechannel
- Design
- The frame
- Extruder and hotend
- Calculations
The reason behind these stages is, that I can split the build process into parts and rather than just buying what I need and find out I need even more parts and then go down the rabbit hole. So if I fail in modernising the mainboard, I may adjust my route or stop here basically.
The end result should somewhat resemble a Creality Ender 3. But due to design changes and choices, it might totally not 🙂
Electronics and firmware:
I need to be sure that the mainboard can be controller by a modern firmware from Marlin or Klipper. I’ll test both firmwares to see if I can still run them on this mainboard. Klipper is preferred for 2 reasons:
1: Klipper uses external computing power, rather than the old 2560 CPU from the K8400. This should improve printing performance, but it will require something like an RaspberryPi 3.
2: I’ll explain why later.
Steppermotor drivers are already attached to the mainboard. But if this build works fine, I will probably upgrade the controllers or install smoothers. The K8400 shakes a lot and makes a lot of noise while printing.
Design:
The overall design, but mainly the design of the frame is important. Sturdiness is key. I have 2 designs, see the drawings below.
The design needs to incorporate the PSU, mainboard, the computing power and all other electronics and wiring harness. Cooling is also required. I’ll be using 12Volt silent fans.
The PSU will also be a challenge as the mainboard operates at about 15Volts, yes 15Volts, also a poor design choice, because 15V and not 12 or 24Volts. I want to install a heated bed, these operate at 24V.
- Heated bed 24V
- Mainboard 15V
- Raspberry Pi 5V
- 3 or 4 Fans 12V
Preferably I install only one PSU and step down to the required voltages. I need to look into that on the best and smallest footprint solution. Using one PSU is a design decision I need to make, because I do not have much space at the base of the printer. The electronics will be located at the bottom of the frame, between the legs. This way the printer will not become top heavy.
The mainboard and RPi3 require additional space and for both of them I need to create a case of some kind, maybe.
The Frame:
The frame itself is made from extruded aluminium. 3D printers have an optimal design size, at least for the print bed. It is 200x200mm, print height will also be about 200mm. The printbed requires a sturdy but lightweight frame. Opposed to the K8400, this design will have 4 adjustable wheels, the K8400 has only 3, which is a design fail if you ask me.
I’ve “made up” two designs that take my design decisions into consideration.
- Sturdy
- Lightweight
- Space for electronics
- Easy to mount equipment and easy build process.
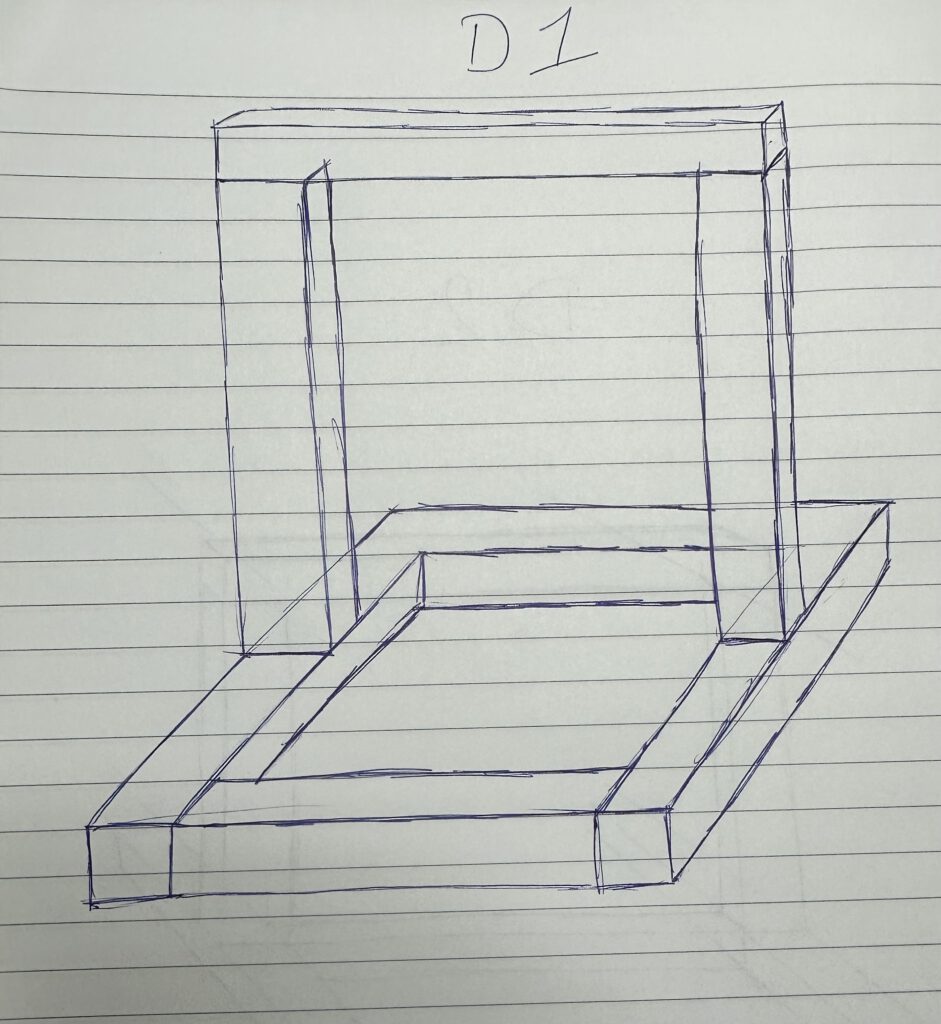
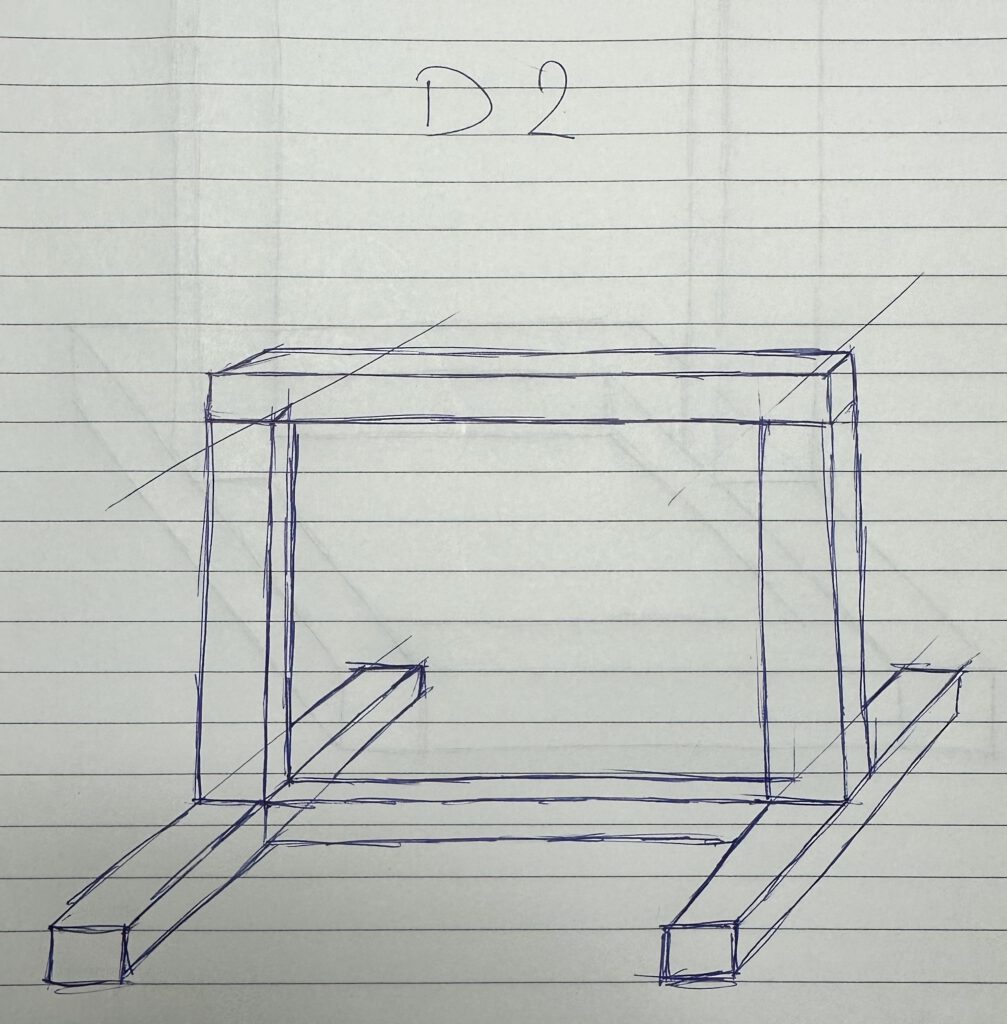
Note that the printbed is not drawn in D1 and D2.
I’ll update the exact dimensions on the go.
The decision is still open. D1 and D2 are opposites of each other in terms of tidiness and accessibility.
Extruder and hotend:
I’ll keep this a simple setup. The extruder I’ll be using is mostly based on the K8400, the hotend will be a E3D V6, because that is what I have.
Calculations
This is probably where I might fail.
Travel distance, print speed, movement speed, belt rotations etc.. It al needs to be calculated. I should start with this, but than the fun is over rather quickly.